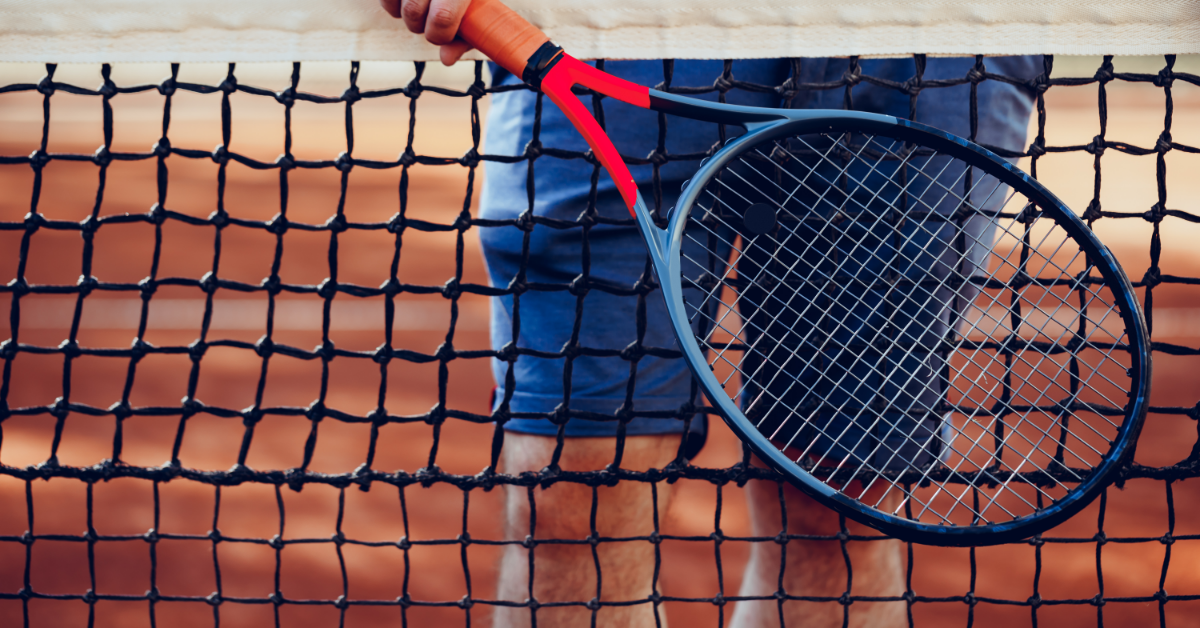
Even if you're not a tennis player, you've probably seen a tennis racket before. But do you know how they're made? Most people don't.
Most people think that tennis rackets are just a piece of wood with some strings attached, but there's actually a lot more that goes into making a great racket.
The first rackets were made of wood, and later players began to experiment with different materials like steel and aluminum. Today, most rackets are made of graphite, a lightweight but strong material that can provide plenty of power and control.
Do you love playing tennis? If so, you're probably curious about how your favorite racket is made. In this article, we will take a comprehensive look at the manufacturing process of tennis rackets. We will discuss the materials that are used and the steps involved in the production process. By the end of this article, you'll have a better understanding of how your racket is made and why it performs the way it does.
We spent countless hours researching the manufacturing process of tennis rackets, and we talked to several experts in the field.
Background of The Manufacturing Process
The manufacturing process of tennis rackets has changed significantly over the years. In the early days of the sport, rackets were made from wood and string. Today, modern rackets are made from a variety of materials, including aluminum, carbon fiber, and Kevlar. The choice of material depends on the desired weight, stiffness, and power of the racket. The production process also varies depending on the type of racket being manufactured. For example, mass-produced entry-level rackets are typically made using injection molding, while high-end custom rackets are usually hand-crafted.
The Materials
As we mentioned earlier, tennis rackets are made from a variety of materials. The most common materials used in racket construction are:
Aluminum
Aluminum is the most popular choice for entry-level rackets due to its affordability and balance of weight, stiffness, and power. Cheaper than composites, aluminum construction provides a friendlier playing experience for those just beginning the game. Additionally, aluminum rackets offer a good mix of weight and power, allowing beginners to generate a decent pace without having to swing too forcefully. Though not as durable as composite materials, aluminum rackets are generally more resistant to damage than entry-level graphite models. For these reasons, players just starting out are often advised to select an aluminum racket.
Graphite
Graphite is a light, strong, and stiff material that is often used in high-end rackets. It allows manufacturers to create lighter-weight rackets without sacrificing power or stiffness. Graphite also provides good vibration dampening, which results in a softer feel on impact and less arm fatigue. The main downside of graphite is its cost; high-end graphite rackets can be quite expensive.
Carbon Fiber
If you've ever played tennis with a racket made of carbon fiber, you know that it can provide a significant performance advantage. This material is prized by racket manufacturers for its exceptional stiffness and strength. When used in a racket frame, carbon fiber helps to transfer energy more efficiently, resulting in increased power and control. In addition, carbon fiber is extremely lightweight, making it easier for players to swing the racket with speed and precision. Carbon fiber's superior performance comes at a price, however, as these rackets can be quite expensive. Nevertheless, many serious players feel that the benefits of carbon fiber are worth the investment.
Kevlar
Kevlar is a polymer that was first developed in the 1960s by DuPont. Since then, it has found a wide range of applications, including everything from tires and bulletproof vests to boat hulls and bicycle frames. In the world of tennis, Kevlar is often used as a reinforcement material in areas where the racket is likely to experience high-stress levels. This can help to increase the racket's power and durability. Additionally, Kevlar can be used in the construction of new types of rackets that are designed to provide players with even more power and control. As such, this synthetic material has helped to revolutionize the game of tennis.
Wood
Though not as popular as it once was, wood is still used in the construction of tennis rackets. This natural material has a number of advantages, including its low cost and high level of stiffness. Additionally, wood is very durable and resistant to damage. However, it is also quite heavy, making it difficult for players to generate speed and power. As a result, most manufacturers now use wood only in the construction of budget-friendly entry-level rackets.
The Steps Involved in The Manufacturing Process
Now that we've looked at the materials used to make tennis rackets let's take a more detailed look at the manufacturing process. Depending on the type of racket being made, this process can vary significantly. However, there are certain steps that are involved in almost all racket production processes. These steps are:
Design and Development
As with any product, the first step in the manufacturing process is design and development. This is where manufacturers come up with new ideas for products and create prototypes. In the case of tennis rackets, designers must consider a number of factors, including weight, balance, stiffness, power, and aerodynamics. Designers must strike a careful balance between these conflicting demands in order to create a racket that is both effective and comfortable to use.
The process is further complicated by the fact that different players have different preferences, and what works for one player may not work for another. As a result, manufacturers must constantly strive to improve upon existing designs in order to stay ahead of the competition.
Once a prototype has been created, it must undergo extensive testing to ensure that it meets all of the necessary criteria. Only after a racket has passed these tests will it be ready for mass production.
Materials Preparation
After the design process is complete, it's time to start gathering the materials that will be used to make the racket. In most cases, this will involve cutting and shaping pieces of wood, aluminum, or carbon fiber. The specific dimensions of these pieces will be determined by the designers and engineers who created the prototype.
Once all of the necessary materials have been gathered, they must be assembled into what is known as a "blank." This blank is effectively a rough version of the finished racket and serves as a template for the rest of the manufacturing process.
Racket Head Molding
The next step is to mold the racket head. This is typically done using a machine that injects molten plastic or metal into a mold. The mold is in the shape of the desired racket head, and once the material has cooled and solidified, it takes on this same shape. Once it has cooled, the racket head is removed from the mold.
After the racket head has been molded, it must be trimmed and shaped to meet the specifications of the design. Once this is done, any holes that need to be present in the racket head (such as those for strings) are drilled into place.
The result is a racket head that is perfectly shaped for optimal performance. While this process may seem simple, it is essential for creating a high-quality racket. Without this crucial step, the racket would not be able to provide the level of power and control that players need to be successful on the court.
Racket Handle Attachment
With the racket head now complete, it's time to attach the handle. In most cases, this is done by inserting one end of the handle into the racket head and then securing it in place with a screw or a piece of adhesive. The type of handle that you use will determine how you need to attach it to the racket head.
For example, if you are using a wooden handle, you will need to insert a screw into the racket head and then screw the handle onto the screw. Alternatively, if you are using an adhesive-backed handle, you will need to simply peel off the backing and stick the handle onto the racket head. Whichever method you use, make sure that the handle is securely attached to the racket head before continuing.
Once the handle has been attached, the next step is to add the grip. This is typically done by wrapping the handle in a layer of leather, rubber, or synthetic material. This grip helps to improve comfort and control while playing.
Stringing
The next step is to string the racket. This process involves threading a series of nylon or steel wires through the holes in the racket head. The number of wires and their gauge (thickness) will vary depending on the type of racket being strung. For example, a recreational racket will typically have 16-18 gauge wire, while a professional-grade racket will have 14-16 gauge wire.
Once all the wires are in place, they are secured at the base of the racket with a clamp. The stringing process is completed by tying the loose ends of the wire together and trimming any excess. Depending on the tension desired, the process can be done by hand or with a machine. For most players, hand-stringing is sufficient, but for those who require a high level of precision, a machine may be necessary.
After the strings have been installed, they must be tensioned to generate the desired level of power and control. Once this is done, the racket is ready for use.
Adding the Final Touches
The final step in the racket manufacturing process is to add the racket's logo and any other desired graphics. This is usually done by silk screening or decal transfer. Silk-screening is a printing process in which ink is forced through a stencil onto the racket surface. Decal transfer involves placing a pre-printed design onto the racket surface and then applying a clear sealant over it.
Both methods allow for a wide range of designs, from simple one-color logos to complex multicolor images. In addition to providing a visual identity for the racket, graphics can also serve as helpful alignment aids for players during their swings. As such, they play an important role in the overall look and performance of the finished racket.